Understanding the Role of Pressure Die Casting Dies Manufacturers
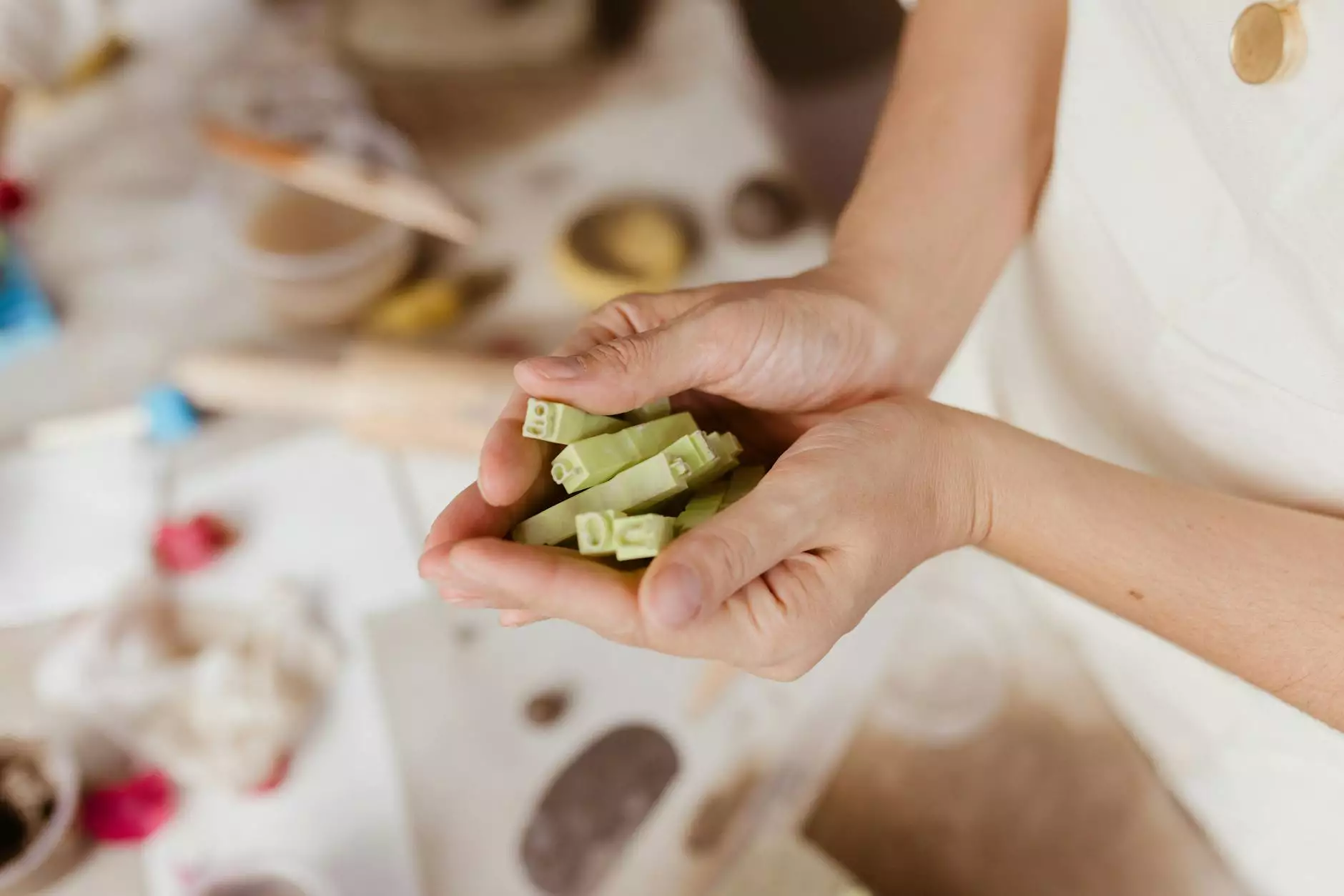
The realm of manufacturing is complex, yet essential to our everyday lives. At the core of many production processes lies a technique known as pressure die casting—a method that embodies efficiency and precision. This article delves into the crucial role played by pressure die casting dies manufacturers and their impact on the metal fabrication industry.
What is Pressure Die Casting?
Pressure die casting is a manufacturing process that involves forcing molten metal under high pressure into a mold cavity. This technique allows manufacturers to produce parts with intricate geometries and excellent surface finishes, making it invaluable in various industries, including automotive, aerospace, and consumer electronics.
The Die Casting Process Explained
The die casting process can be broken down into several key steps:
- Preparation: The die is prepared by applying lubricant to ensure easy release of the cast part.
- Melting: Metal is melted in a furnace, reaching a temperature suitable for casting.
- Injection: The molten metal is injected into the die under high pressure.
- Cooling: The metal cools and solidifies within the die, taking its final shape.
- Ejection: Once cooled, the die is opened, and the finished part is ejected.
The Importance of Pressure Die Casting Dies Manufacturers
Die manufacturers play a pivotal role in the success of any pressure die casting operation. Their expertise ensures that dies are crafted to withstand high temperatures and pressures while producing consistently high-quality parts.
Quality and Precision
One of the most critical aspects of pressure die casting dies manufacturers is their commitment to quality and precision. The dies they produce must meet stringent specifications to ensure that the final products are defect-free and dimensionally accurate. This means:
- Utilizing high-grade materials to withstand thermal and mechanical stresses.
- Employing advanced engineering techniques to design dies that facilitate efficient metal flow.
- Implementing rigorous quality control measures throughout the manufacturing process.
Benefits of Using Pressure Die Casting
Engaging with experienced pressure die casting dies manufacturers provides several advantages:
1. Cost Efficiency
Pressure die casting reduces material waste as the process can produce intricate parts with minimal excess material. This efficiency translates into cost savings for manufacturers.
2. High Production Rates
Due to its rapid cycle times, pressure die casting allows manufacturers to produce large volumes of parts in a short duration, meeting high demand without compromising on quality.
3. Excellent Surface Finish
Parts produced through pressure die casting often require little to no additional finishing. This aspect saves both time and money in the production process.
4. Superior Mechanical Properties
The process enables manufacturers to create components with enhanced strength and durability, making them suitable for rigorous applications.