The Significance of a Plastic Injection Mold Company in Modern Manufacturing
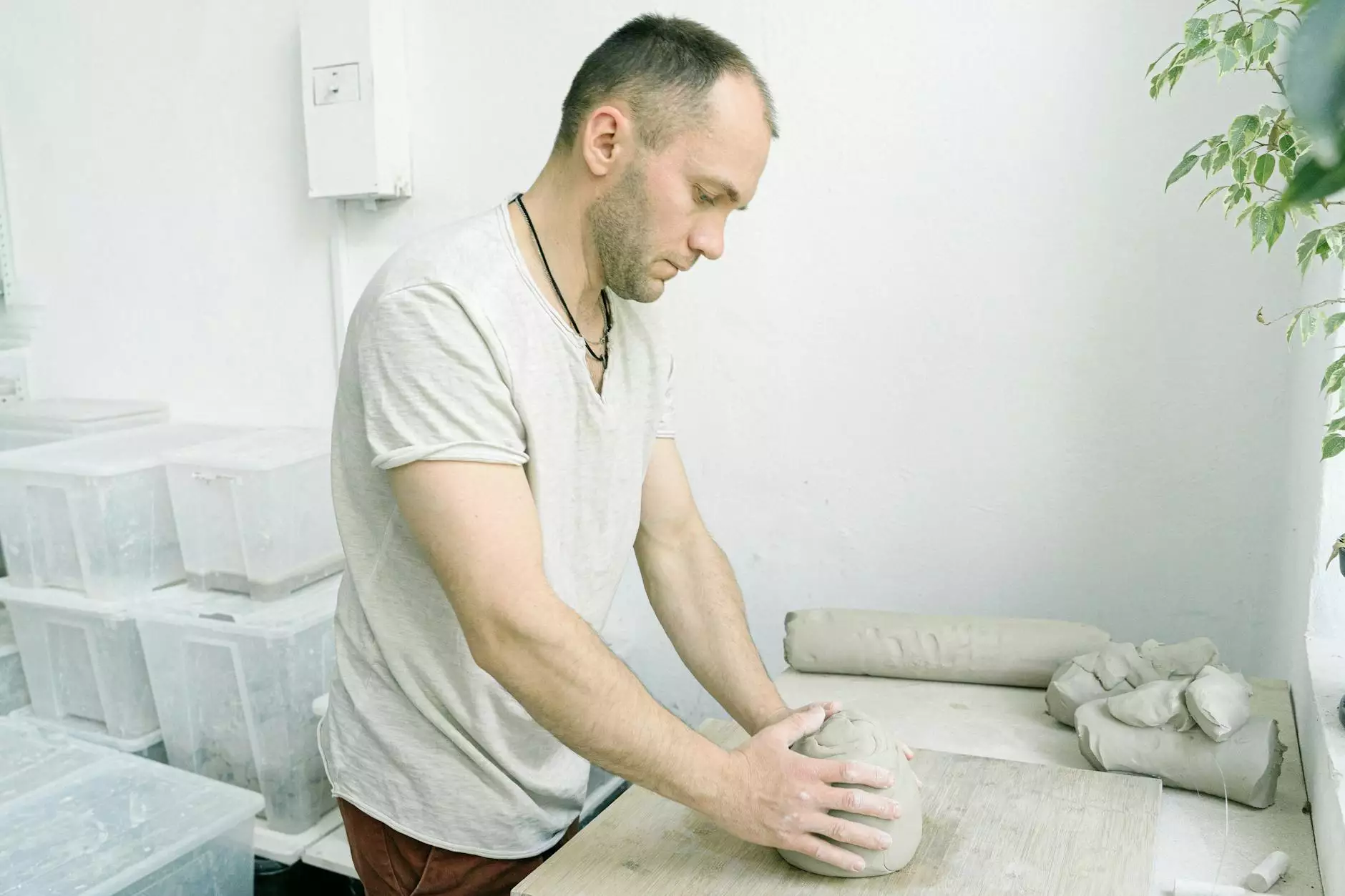
Plastic injection molding has emerged as one of the most impactful manufacturing processes in the contemporary industrial landscape. A plastic injection mold company plays a pivotal role in shaping not just plastic components, but also the future of various industries including automotive, medical, consumer goods, and more. This article aims to explore the significance, processes, and innovations led by plastic injection mold companies, specifically focusing on DeepMould.net and its contributions to the field of metal fabrication and plastic injection molding.
What is Plastic Injection Molding?
At its core, plastic injection molding is a manufacturing technique used for producing parts by injecting molten material into a mold. This process has become a preferred choice due to its efficiency and capability to produce intricate designs with high precision.
History and Evolution
The origins of plastic injection molding date back to the 19th century. In 1872, John Wesley Hyatt patented the process, which has significantly transformed into the advanced technology we have today. The growth of this industry aligns with the innovation and demand for plastic products, proving the sustainability and efficiency of the process.
Why Choose a Plastic Injection Mold Company?
Partnering with a reputable plastic injection mold company is crucial for any business looking to manufacture plastic products. Here are several compelling reasons:
- Expertise and Knowledge: Professionals in the field possess the technical know-how that can drive project success.
- Quality Assurance: Established companies ensure that products meet stringent quality standards.
- Advanced Technology: Access to state-of-the-art facilities and machinery boosts productivity.
- Cost-Effectiveness: Efficient processes reduce waste and production costs, appealing to budget-conscious businesses.
- Customization: Flexibility to create tailored solutions based on specific customer needs.
Key Processes Involved in Plastic Injection Molding
The process of plastic injection molding can be broken down into a series of methodical steps:
1. Material Selection
The journey begins with selecting the right type of plastic resin. Various materials like ABS, polypropylene, and polycarbonate are chosen based on their properties suitable for the intended application.
2. Mold Design
A robust mold design is crucial for the success of any injection molding project. This entails creating a digital prototype using CAD software, allowing for modifications before any physical mold is crafted.
3. Mold Manufacturing
Once approved, the mold is produced, typically out of steel or aluminum. This stage demands precision and expert skills to ensure that the mold is capable of producing high-quality parts.
4. Injection
During this critical phase, the selected resin is heated until it liquefies and is then injected into the mold under high pressure. This ensures that every part of the mold is filled evenly.
5. Cooling
After injection, the material is allowed to cool and solidify inside the mold. This cooling time can significantly impact the overall cycle time and productivity.
6. Ejection
Once the plastic has cooled, the mold opens to eject the finished product. This is where precision engineering by a plastic injection mold company truly shines, as any flaws at this stage can lead to waste and additional costs.
The Benefits of Using Plastic Injection Molding
The advantages of plastic injection molding are vast and multifaceted:
- High Efficiency: Injection molding offers rapid production, making it ideal for mass production.
- Consistency: Once a mold is created, the process can replicate the same product with exceptional uniformity.
- Material Versatility: Various materials can be used to meet the requirements of different product lines.
- Intricate Designs: Complex geometries can often be created that would be difficult or impossible with other methods.
- Less Waste: This process is efficient, leading to minimal waste materials compared to alternative manufacturing processes.
DeepMould.net: Leading the Way in Plastic Injection Molding
DeepMould.net stands out as a premier plastic injection mold company within the metal fabrication sector. By combining innovation with experience, DeepMould has established a reputation for quality and reliability.
Innovative Approaches
DeepMould employs cutting-edge technology and techniques, ensuring their molds meet the highest standards. Their commitment to continuous improvement and adoption of the latest advancements means that customers can trust they are receiving the best possible service.
Commitment to Quality
At DeepMould, quality is not merely a goal—it’s a promise. Through rigorous testing and quality control checks, they ensure that every product manufactured meets or exceeds expectations, providing peace of mind to clients.
Industries Benefiting from Plastic Injection Molding
The versatility and effectiveness of plastic injection molding make it a favored choice across various industries, including:
- Automotive: Parts like dashboards, panels, and other components are manufactured using this technique for its durability and lightweight properties.
- Medical: Production of medical devices and components where precision and hygiene are critical.
- Consumer Goods: Everyday products such as toys, household items, and electronics all benefit from custom plastic parts.
- Packaging: Breathtaking advancements in packaging design are achievable through injection molding.
Future Trends in Plastic Injection Molding
The future of plastic injection molding is bright, driven by technological advancements and changing market demands. Notable trends include:
1. Eco-Friendly Practices
As sustainability becomes a priority, many companies are integrating recyclable materials and eco-friendly practices into their processes.
2. Automation and Robotics
The use of automation in injection molding will increase efficiency and product output, while reducing labor-intensive tasks.
3. Enhanced Design Capabilities
With advancements in software and modeling techniques, the capacity to create complex designs will only continue to grow.
Conclusion
In summary, the role of a plastic injection mold company is incredibly significant in the modern manufacturing landscape. With organizations like DeepMould.net leading the charge, businesses across various industries can rely on precise, efficient, and cost-effective solutions to their plastic manufacturing needs. As technology continues to evolve, the future of plastic injection molding appears poised for even greater innovation and sustainability, making it an indispensable part of today’s economy.